Advanced Virtual Aptitude and Training Application in Real Time
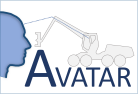
Coordinator: Dirk Jaeger, Georg-August Universität Göttingen, Germany
dirk.jaeger (at) uni-goettingen.de
Other partners: NO, SE
Project duration: 03/2019-10/2022
Project abstract:
The objective of the AVATAR project was to develop an assistance and coaching system for forest machine operators to increase operational efficiency and perceived job satisfaction in mechanised timber harvesting – while reducing mental workload. Through this, the project should contribute to efficiency improvements of CTL operations for enhanced timber utilization at higher value-added resource recovery, alongside occupational health and safety, and thus support the implementation of a sustainable and competitive bio-economy in Europe.
To identify relevant elements and features of the assistance system, project partners held a series of exploratory interviews with professional harvester operators from Sweden, Norway, and Germany. In order to find out which factors are important for the quality of work, which operator behaviour is beneficial and which is not, and also what would be helpful as part of a continuous feedback system.
That system aimed to support machine operators during harvesting and forwarding operations to reduce mental strain and raise efficiency as well as quality of work.
To provide the feedback system with necessary data to then give helpful support to machine operators several algorithms and sensors were developed and successfully tested:
- Algorithms enabling automatic detection of work elements and working methods for forwarders and harvesters.
- A model for the prediction of harvester measurement precision for raised value recovery.
- A sensor platform to localize the exact machine position even in a GNSS-denied environment and characterize the operating environment of the machine via LiDAR.
- Algorithms to recognise standing trees in the vicinity as well as the machine itself, its crane and the harvester head.
Another aspect was to identify optimal working ranges and crane angles of forest machines for advising operators with respect to enhanced efficiency of machine operations and improved collaboration between timber harvesters and forwarders.
Machine operators were provided with relevant information using a head-up display in the cabin during an actual timber harvesting operation in Germany.
Project website: link
Twitter: link
Project presentation at ForestValue kick-off seminar 23-24 May 2019: pdf
Stakeholder Article 1 AVATAR – Exploring harvester operators’ need for feedback
Stakeholder Article 2 AVATAR – Real time follow-up of the precision of the harvesters’ diameter sensing
Stakeholder Article 3 AVATAR – Automatic detection of work elements of forestry machines
Stakeholder Article 4 AVATAR – Demonstration of real-time sensor-based decision support for forest machine operators
Stakeholder Article 5 AVATAR – Boom tip control: Mere comfort or skill booster?
Stakeholder Article 6 AVATAR – Operator assistance systems and their suitability for improving efficiency of highly mechanized timber harvesting systems